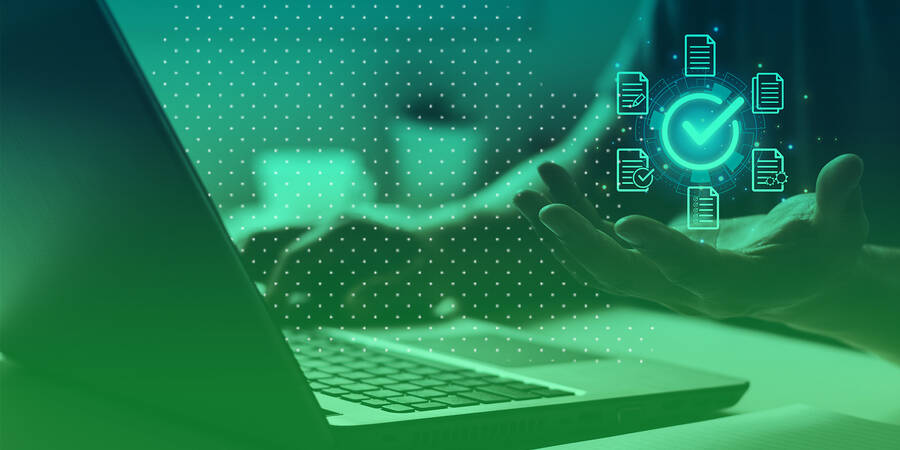
Advancing quality management through PLM technologies
Best-in-class industrial leaders are driving a transformative shift in addressing quality management. These forward-looking organizations are leveraging cutting-edge technologies to enhance efficiency and effectiveness. Through digital transformation, quality management benefits from advanced data analytics, cloud-based systems, machine learning, and artificial intelligence, leading to more informed decision-making and proactive problem-solving. It also mitigates compliance risks by ensuring adherence to industry standards and regulations. While these solutions are helping the best-in-class extend their advantage over competitors, the journey toward digital transformation is not without its challenges. Let’s explore the nuances of digital transformation in quality management, its impact, and how to avoid obstacles that lie ahead.
What is digital transformation in quality management?
Digital transformation in quality management refers to the integration of digital technologies into all aspects of quality control processes, fundamentally changing how businesses operate and deliver value to customers. The best-in-class recognize this transformation as a top priority because it helps ensure the following outcomes:
Enhanced customer experience
By leveraging digital transformation, organizations can create significant value for the customer experience. With 3D technologies, customers and suppliers can collaborate on product development across countries and continents. Real-time data access allows monitoring of production and after-sales processes, leading to better customer experiences.
Technologies like 3D modeling enable collaboration across borders and enhance product development. Access to real-time data ensures that production and after-sales services are constantly monitored and improved, leading to an exceptional customer experience. This aligns with the benefits of cloud-based quality management systems, which allow for continuous improvement and process standardization and are accessible from anywhere, thus ensuring high standards and efficient processes.
Quality control and assurance
The adoption of digital technologies minimizes human error in quality management. Quality managers can use digital tools to improve quality control and assurance processes. Quality managers can utilize digital tools to bolster quality control and assurance processes, which is a testament to the benefits of advanced data analytics and increased machine learning in digital quality management (DQM) systems. These tools provide predictive insights and automate quality checks, ensuring higher accuracy and reliability.
Cloud-based quality management systems
These systems facilitate continuous improvement efforts, process standardization, compliance, and other quality initiatives from any location. In addition to upholding high standards and efficient processes, quality management often serves as a catalyst for additional digital transformation.
What is the impact of digital transformation in quality management?
Digital transformation and quality management are a mutually beneficial combination, having several positive impacts on a given organization:
• Efficiency and automation: Digital tools streamline processes, automate repetitive tasks, and reduce manual errors. This efficiency translates to better quality control and faster response times.
• Data-driven decision making: Real-time data collection and analysis allow quality managers to make informed decisions. Predictive analytics can identify potential quality issues before they escalate.
• Collaboration and communication: Digital platforms enable seamless collaboration across teams, suppliers, and customers. Quality-related information can be shared instantly, bolstering communication and fast problem-solving.
• Traceability and compliance: Digital systems track product lifecycles, ensuring traceability from raw materials to end-users. This makes compliance with industry standards and regulations much easier to maintain.
• Continuous improvement: Digital tools facilitate continuous improvement initiatives. Quality managers can monitor performance metrics, identify bottlenecks, and implement corrective actions.
Digital transformation enhances quality management by promoting efficiency, data-driven insights, collaboration, and compliance. Discover the importance of digital transformation and its strongest drivers for success on PTC’s Industry Insights.
The capabilities of quality management achieved through digital transformation
Quality management is hardly a new discipline, but digital transformation is a game changer for quality management systems. It introduces a multitude of benefits that enhance the overall efficiency and effectiveness of a manufacturing environment. These benefits collectively contribute to a robust quality management system that is resilient, responsive, and capable of driving continuous improvement. They ensure that quality management is not just a compliance activity but a strategic advantage that can lead to better products, satisfied customers, and a stronger market position.
Advanced data analytics
The integration of advanced data analytics into quality management allows for a deeper understanding of processes and outcomes. It enables the identification of patterns and trends that can lead to more informed decision-making and proactive measures to maintain high-quality standards.
Cloud-based quality management systems
Cloud-based solutions offer scalable and flexible platforms that can be accessed from anywhere at any time. This ensures that quality management processes are not confined to a single location and can adapt to the dynamic needs of the business.
Increase in machine learning
Machine learning algorithms can predict potential quality issues before they occur, allowing for preemptive action to be taken. This not only saves time and resources but also helps in maintaining a consistent quality of products or services.
Artificial intelligence
As artificial intelligence (AI) becomes more prevalent, it’s important to structure your data for AI consumption. Some anticipated AI applications include automating complex quality management tasks, reducing the need for manual intervention, and providing insights to support continuous improvement efforts.
How does digital quality management mitigate compliance risks?
Digital quality management systems significantly mitigate compliance risks by integrating various compliance-related processes and ensuring adherence to regulatory standards. Through DQM solutions, compliance is not just a one-time check but an integrated part of the quality management process, thereby significantly reducing the risk of non-compliance and the associated penalties.
Streamlined compliance management
DQM systems provide a centralized platform for managing all compliance-related activities, ensuring that nothing falls through the cracks. This includes tracking regulatory changes, managing documentation, and ensuring that all processes are up to date with the latest compliance requirements.
Proactive risk identification
By leveraging advanced data analytics, these systems can identify potential compliance risks before they become issues. This proactive approach allows organizations to address risks promptly and avoid non-compliance.
Automated documentation
Digital systems automate the creation and maintenance of essential compliance documents, reducing the risk of human error and ensuring that all necessary documentation is accurate and readily available for audits.
Enhanced traceability
With a DQM system, every aspect of the product lifecycle is traceable. This provides a clear audit trail from design to delivery that can be easily accessed during inspections.
Continuous improvement
Digital transformation enables a culture of continuous improvement, where insights from data analytics and machine learning are used to refine and enhance existing processes. This not only improves quality but also ensures that compliance is maintained as processes evolve.
What challenges are faced when implementing digital transformation in quality management?
Implementing digital transformation in quality management presents a set of challenges that organizations need to navigate carefully to ensure a successful transition. Fortunately, once we identify and anticipate potential bottlenecks, it’s much easier to avoid them.
• Cultural resistance: Change can be difficult, and there may be resistance from employees who are accustomed to traditional methods. Overcoming this requires effective change management and communication strategies.
• Data integration: Ensuring data consistency and quality across different systems, such as ERP and PLM, can be complex. Discrepancies can lead to errors and inefficiencies.
• System compatibility: Integrating new digital tools with existing systems can be challenging, especially if the current infrastructure is outdated or incompatible with new technologies.
• Training and skill development: Employees must be trained to use new digital tools effectively. This can be time-consuming and requires investment in skill development but is nonetheless critical to digital transformation success.
• Cybersecurity risks: The increased use of digital systems raises the risk of cyber threats. Organizations must implement robust security measures that scale with their digital transformation efforts in order to protect sensitive data.
• Cost: Implementing digital transformation initiatives can be costly, and organizations must ensure they have the budget to support the transition and ongoing maintenance.
• Regulatory compliance: Maneuvering the complex regulatory landscape and ensuring that DQM systems comply with all relevant laws and standards is crucial.
These challenges highlight the importance of a well-planned and executed digital transformation strategy that removes or minimizes these potential hurdles. Part of that planning is careful vetting of technologies that can deliver the best outcomes while addressing these potential challenges.
How does digital transformation in quality management impact different industries?
Each industry has unique challenges and opportunities, requiring a similarly distinct digital transformation journey. Whether it’s enhancing the driver experience in automotive, or enabling digital thread in industrial equipment, the common goal is improving quality management to achieve better products, services, and business outcomes.
Automotive
Digital transformation is reshaping the automotive industry by introducing electric vehicles, advanced driver assistance systems, software-defined cars, and new in-vehicle displays. Through digital transformation, the automotive industry can improve product quality by enabling better collaboration across teams and enhancing product development with technologies like 3D modeling and PLM.
Medical devices
For medical devices, digital transformation helps manage increasing complexity, competitive pressures, and regulatory compliance. It enables medical device companies to innovate and accelerate speed to market while managing documentation and compliance demand—which is particularly important given the stringent regulations in this industry.
Industrial equipment
In the industrial equipment sector, digital transformation in quality management facilitates workforce adaptation to new digital ways, orchestrates ecosystems for successful execution, and helps achieve value quickly with scalable solutions. Electronics and High-Tech The electronics and high-tech industry benefits from digital transformation through real-time production performance monitoring, enterprise plant benchmarking, and scalable production management. These advancements are crucial for improving quality and accelerating time to market, which is essential for success in this rapidly evolving sector.
Oil and gas
Digital transformation in quality management within the oil and gas industry can lead to smarter capital projects, better equipment health monitoring, and more efficient operations that align with environmental and economic goals. It also supports workforce adaptation and the industry’s move toward decarbonization.
Aerospace and defense
In the aerospace and defense industry, digital transformation enhances the entire product lifecycle through a digital thread by improving both compliance and complexity and enabling predictive maintenance. It also increases workforce efficiency and impacts service organizations by improving maintenance quality and speed, while aiding in cost management and strategic planning.
Retail
Meeting customer expectations, delivering individualized experiences at scale, and operating at market speed are critical for the retail space. Digital transformation in quality management helps reduce cycle time, understand customer usage patterns for better product designs, and manage complex supply chains to maintain customer loyalty and stay competitive.
Achieve better quality through digital transformation
Go beyond the average benefits of a quality management system by empowering your quality initiatives through digital transformation. A PLM platform is the best approach to quality through digital transformation by supporting change management efficiency, fast responses to internal and market pressures, and improved product quality. PLM can also enable global teams to collaborate through shared product information, ultimately driving superior business performance.